Optimal Production Scheduling
- Marco Better
- Apr 29, 2024
- 2 min read
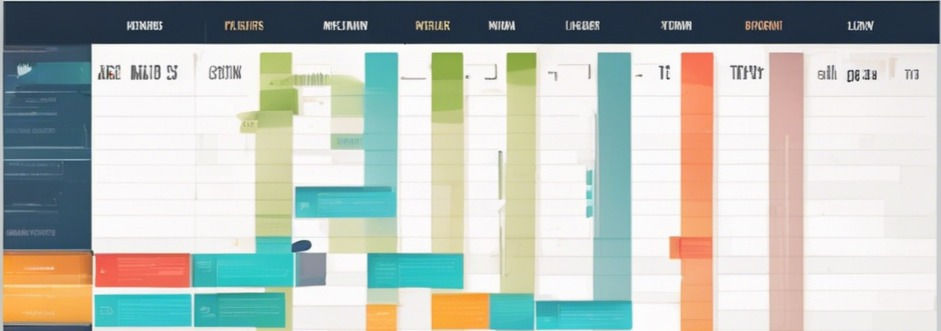
Commercial software offerings for production scheduling are rife with terms and labels that are meant to impress potential customers into the belief that theirs is the best approach to production scheduling. Some software vendors offer “Advanced Planning and Scheduling (APS)”; others offer “Algorithm Based Scheduling (ABS)”; many ERP systems offer their own module for planning and scheduling, touting features like “Master Production Scheduling and Planning (MPS or MPSP)”. No matter how impressive the label, many of these offerings – if not all – suggest that there is a one-size-fits-all approach to production scheduling. Nothing could be farther from the truth.
Invariably, these off-the-shelf software products apply relatively simple, rule-based heuristics that sequence tasks according to the characteristics of the task; for example, its due date or its priority, its processing time, or how much time is left to complete the task. More sophisticated offers may combine two or more of these rules into ratios or simple functions, but the basic concept remains the same – there is a single-minded, deterministic approach to sequencing tasks on resources. Although appealing for their simplicity and intuitive nature (i.e., it is intuitive to order tasks based on when they are due), these methods usually produce inferior results because they tend to ignore other attributes of the tasks, such as penalties for tardiness, interactions with other tasks, resource constraints, changeover or setup times, etc.
These rule-based systems may be adequate for very straightforward operations. In more complex situations, optimization-based approaches should be used. Optimization-based methods use mathematical programming techniques to find the optimal solution – the sizing of jobs, lots, or batches; the assignment of those jobs or flows to multiple production lines; and the optimal sequencing of those jobs or flows on each production line in order to maximize or minimize some set of key metrics, like throughput or operating cost. Highly complex real-world systems, furthermore, require a combination of these mathematical approaches with heuristic solution techniques and, often, simulation modeling – i.e., digital twin – approaches.
BBA’s solution framework goes beyond rule-based approaches to offer Optimal Production Scheduling (OPS). In this case, the label is not just meant to impress – it tells the truth. BBA utilizes true mathematical optimization to enable optimal decision making through powerful algorithmic and analytical techniques, including math programming, meta-heuristic strategies, and digital twin simulation modeling. While BBA’s solutions consist of a core software platform that conforms to a wide variety of manufacturing settings, the algorithms in our technology are configured to reflect the specific conditions, constraints, and characteristics of each of our client’s operation.
We design our technology to meet a growing need from companies with highly complex planning and operational scheduling requirements. These companies are typically dissatisfied with their current scheduling capabilities, be it off-the-shelf systems or large manual spreadsheets, and are seeking to develop a competitive advantage through optimal production scheduling.
For additional information about the benefits other clients have derived from applying optimal production scheduling in their manufacturing environments, please visit www.bettersolv.com, or get in touch with us at https://www.bettersolv.com/letstalk.
Comments